Perigos em disfarce
CATEGORIAS:
Clayton A. Francis, Zeeco, EUA, explica por que os maiores impactos ambientais dos equipamentos de queima podem parecer inofensivos.
Às vezes, coisas que parecem inócuas podem ser prejudiciais. De acordo com a Organização Mundial da Saúde, mais jovens de hoje correm risco de perda auditiva devido a seus aparelhos de áudio pessoais do que devido ao volume de concertos e locais de música.1 É a exposição comum, aparentemente insignificante, que tem o maior impacto, não, como seria de se esperar, a explosão infrequente. Este fenômeno se aplica a outros aspectos da vida cotidiana, incluindo o impacto de certos equipamentos de processo.
Membros da comunidade e especialistas em regulamentação têm se perguntado, às vezes, se os flares são eficazes em seu trabalho de descarte de gás confiável, seguro e ambientalmente responsável. Testes extensivos, ao longo de quatro décadas, confirmaram que os flares operados adequadamente protegem de forma confiável o meio ambiente, bem como os equipamentos e o pessoal em uma instalação operacional. Os testes foram realizados principalmente em cenários de operação ideal da ponta do flare e de seus fluxos de utilidades. Entretanto, fatores tão variados como treinamento insuficiente, falta de medição do processo ou outros obstáculos operacionais podem facilmente levar à operação ineficiente e ineficaz de um processo flare.
Ao considerar a complexidade adicional das tecnologias de queima sem fumaça, outro fator operacional é a relação crítica entre as taxas de fluxo do gás flare e do meio de injeção sem fumaça. Quando é aplicado muito vapor ou ar - os dois meios de injeção sem fumaça mais comuns - a zona de combustão pode ser diluída até que a eficiência da combustão seja reduzida ou até mesmo interrompida completamente. Além de garantir que o projeto inicial do flare esteja em conformidade com a legislação ambiental, é imperativo que o projeto do flare ofereça proteção contra a liberação de hidrocarbonetos não queimados, mesmo com a baixa taxa normal de fluxo/purga do flare.
Uma dificuldade inerente às tecnologias de flare sem fumaça é que são necessários fluxos mínimos de utilidade do meio de injeção sem fumaça para proteger o equipamento de combustão contra danos térmicos. Esses fluxos mínimos, sejam eles um fluxo especificado pelo fabricante do equipamento ou uma limitação pragmática de abertura de cama no equipamento, são um pouco altos quando comparados ao gás de purga combustível mínimo que flui para o flare. Esse desequilíbrio entre a taxa mínima de flare e o fluxo comparativamente grande do meio inerte sem fumaça pode ser devastador para a eficiência da combustão. Como os flares raramente fluem com taxas de perturbação significativas, essa incômoda ineficiência de combustão nas taxas de purga constitui a operação normal, hora a hora. Dessa forma, o aparentemente inócuo compreende o maior impacto ambiental do equipamento de queima.
Os riscos do desequilíbrio entre o meio de injeção sem fumaça e o gás flare foram estudados e identificados por pesquisadores e órgãos reguladores, levando a regulamentações nos EUA que monitoram e controlam de perto essa proporção para garantir a combustão adequada, mesmo em turndown.2,3 Para as tecnologias convencionais de ponta sem fumaça flare , é necessário um aumento nas taxas de purga de combustível para atender às regulamentações de eficiência de combustão em operação normal sem upset, levando a um aumento no consumo de gás combustível e a desafios para as licenças de operação existentes. Com a revelação de que é provável que haja tanto impacto negativo em uma operação normal, o desequilíbrio entre a injeção mínima de vapor e as taxas de purga de gás flare deve ser atenuado.
Reduzindo o consumo de vapor
As chamas são feitas sem fumaça, garantindo que haja ar suficiente e oxigênio arrastado disponíveis e misturados com o fluxo de hidrocarbonetos, de modo que toda a ligação de carbono com carbono seja oxidada. Com as tecnologias de vapor flare , não é o vapor em si que torna a chama sem fumaça, mas principalmente o ar impulsionado e arrastado pelo fluxo de vapor. Os avanços na tecnologia de vapor flare , seja visando à redução do consumo de vapor ou ao desempenho aprimorado da zona de combustão no turndown, começam com o aumento da eficiência com a qual o ar é transportado pelo vapor.
Zeeco Os engenheiros da KPMG desenvolveram a tecnologia SteamForce HC flare para resolver problemas ambientais por meio de um mecanismo eficiente de injeção de vapor. A redução do consumo de vapor tem vários efeitos positivos sobre os custos operacionais, os impactos ambientais e a conformidade operacional. No novo projeto, um único riser de gás flare é distribuído entre vários bicos de vapor. Os conjuntos de bicos são compostos por um venturi com duto de ar cercado concentricamente por um anel de gás flare (Figura 1). Cada bocal utiliza a injeção de vapor como força motriz em sua base e é cercado no perímetro por um anel de jato para garantir a mistura completa e a interação entre o gás flare e o ar de combustão redutor de fumaça.
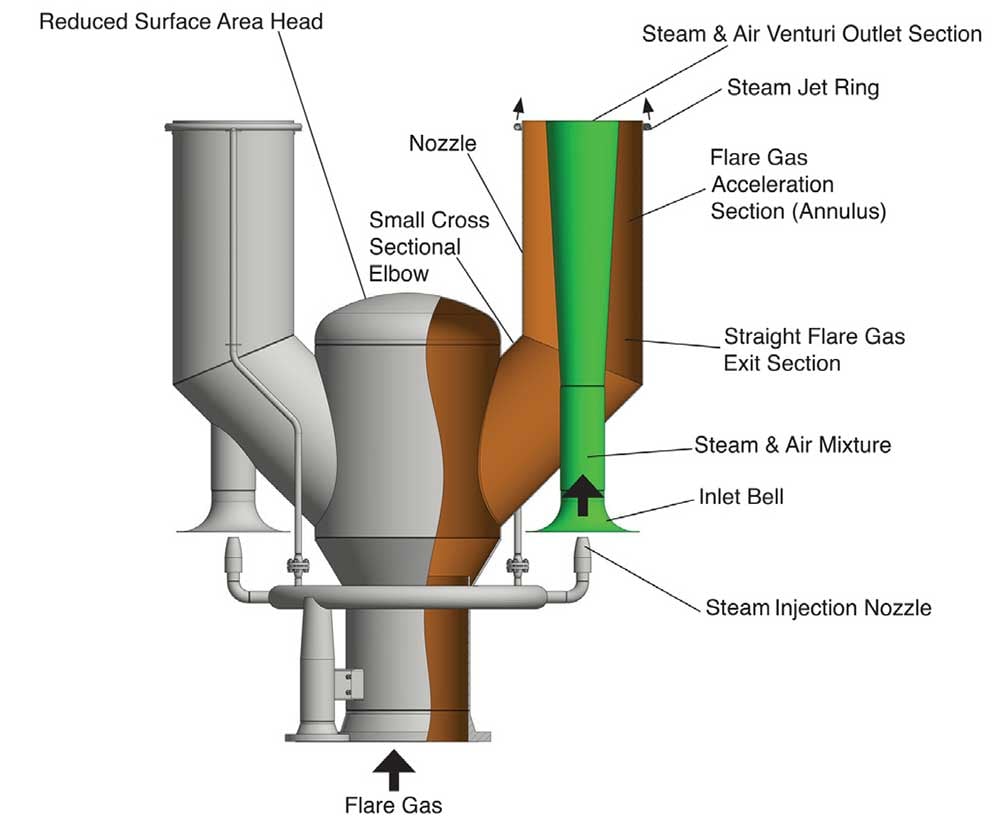
Tecnologia de Injeção de Vapor
Nas primeiras tecnologias de injeção de vapor, um injetor impulsiona o ar ambiente para a zona de combustão, na maioria das vezes com um coletor de injetores ao redor do perímetro da ponta. O uso de tubos de vapor/ar (S/A) aumenta a eficiência da injeção de ar para vapor ao coletar o ar com um sino de entrada e, em seguida, transportar esse volume de ar por um tubo até o núcleo da zona de combustão. O aumento do volume de ar e sua implantação em regiões de difícil acesso do gás flare têm sido a base por trás da maioria das pontas de vapor de alta capacidade flare há décadas. No entanto, duas ineficiências no sistema persistiram: os tubos S/A exigiam uma curvatura para direcionar corretamente o fluxo, o que diminui a eficiência, e o tubo tem um diâmetro consistente em todo o seu comprimento (Figura 2, à esquerda).
Altas velocidades no tubo S/A quando operado em alta capacidade criam perdas por arraste e queda de pressão, limitando a entrega total de ar para cada tubo. Várias tecnologias mais novas estão incorporando tubos retos para melhor desempenho; entretanto, o fluxo ainda é limitado e as eficiências limitadas na configuração consistência-diâmetro (Figura 2, à direita). Os Venturis são dispositivos bem conhecidos e têm sido utilizados em equipamentos em plantas de processo para comprimir, impulsionar ou multiplicar fluxos.
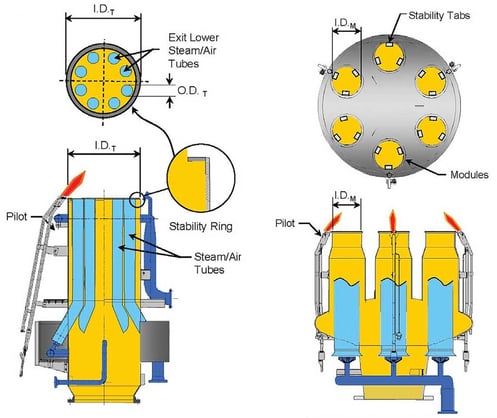
Os venturis verdadeiros só recentemente foram incorporados às pontas de vapor do flare para propulsão a ar. O cone de expansão a jusante da seção de compressão do venturi evita o arrasto e a restrição do projeto de tubo de diâmetro reto (Figura 3).
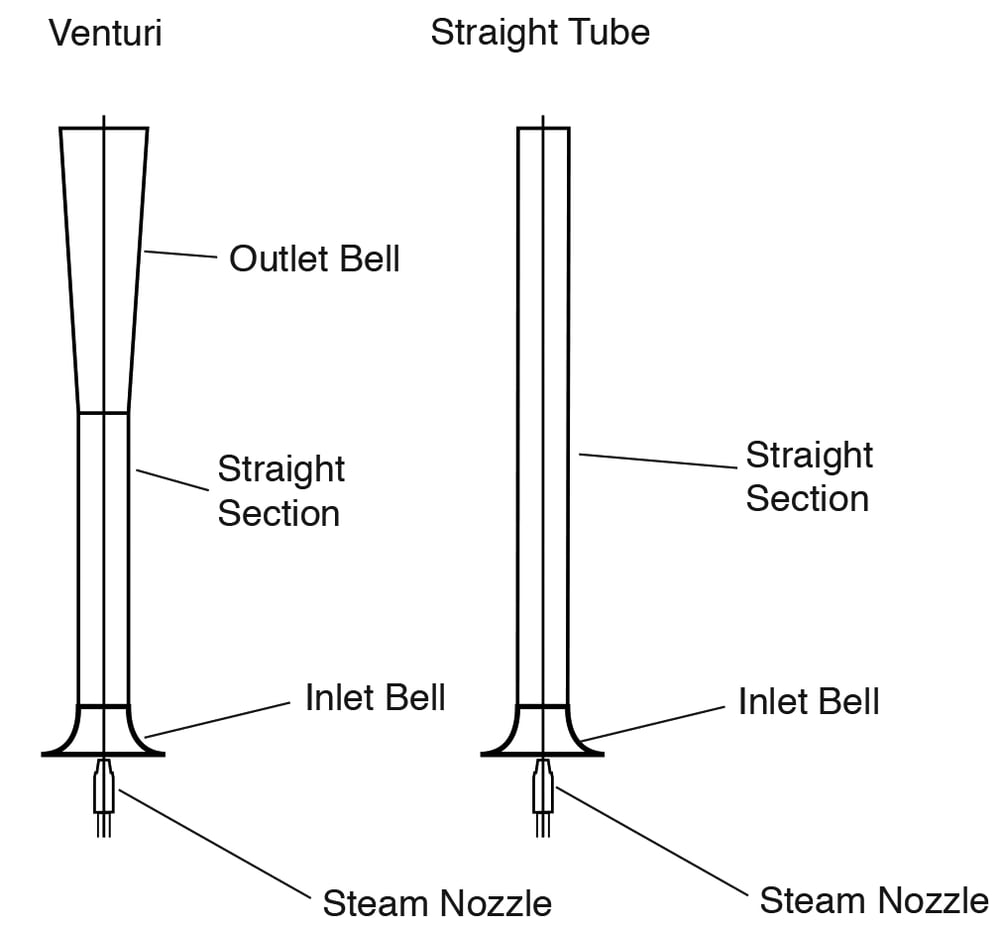
Em geral, o impulso do vapor ejetado do bocal de vapor (em ambos os dispositivos) puxa o ar ao redor para dentro da campainha de entrada. A mistura de ar e vapor flui então através da seção reta, com o fluxo se desenvolvendo. No projeto venturi, o fluxo então se move através do sino de saída que gradualmente aumenta na área de saída, diminuindo a pressão, permitindo que mais fluxo se mova através do sistema. Através de testes empíricos, este projeto de tubo demonstrou um aumento de até 80% no volume de ar para o mesmo fluxo de vapor para um tubo S/A de tamanho semelhante (Figura 4). Este aumento da propulsão do ar resulta em economias significativas de vapor em capacidades sem fumaça (perturbação), mas mais importante ainda, o consumo reduzido de vapor também é aplicável em taxas normais de purga diária.
Figura 4. Para uma vazão de vapor de 3.427 lb/h, o projeto venturi sem pré-mistura pode puxar 49.572 lb/h de ar em comparação com 27.468 lb/h de ar para um dispositivo de tubo reto com pré-mistura de gás flare , vapor e ar. Além disso, o dispositivo venturi atingiu uma relação de massa de 14,47 lb de ar por 1 lb de vapor em comparação com 8,06 lb de ar por 1 lb de vapor para o dispositivo de tubo reto.
Melhorar o acesso ao suprimento de ar ambiente nas configurações do flare é um conceito que comprovadamente funciona em tochas terrestres de vários pontos, tecnologias sônicas de vários braços e outras. Com pontos de injeção adicionais, os limites de interação entre o gás flare e o oxigênio disponível aumentam, de modo que mais oxigênio é puxado para a zona de combustão. Só recentemente esse conceito foi aplicado aos flares de vapor, já que tradicionalmente eles eram um único barril grande. A distribuição do fluxo de hidrocarbonetos entre vários conjuntos de bicos multiplica a proporção de ar ambiente em contato com os fluxos de hidrocarbonetos no flare. Essa configuração cria um fluxo anular para o gás flare (Figura 1), ou seja, ele é cercado por ar nos perímetros interno e externo. O encapsulamento do gás dessa forma garante uma interação superior entre o vapor e o ar, aumentando ainda mais a capacidade de não gerar fumaça. Em última análise, as tecnologias de vapor flare são comparadas pela relação de injeção de massa de vapor para hidrocarboneto (S/HC) necessária para tornar as composições de gás individuais sem fumaça. Ao usar o propileno como meio de gás de teste, as taxas S/HC esperadas são de 0,55 para a configuração tradicional de vapor somente com injeção superior flare e de 0,38 para projetos de tubos S/A curvos. Por outro lado, um projeto anular requer uma taxa de 0,25 kg de vapor para cada 1 kg de propileno queimado sem fumaça (Figura 5).
Figura 5. A figura acima mostra a economia no consumo de vapor com o uso de um SteamForce HC flare em comparação com o uso de um tubo S/A dobrado convencional ou da ponta superior de vapor flare .
Flare O desempenho é normalmente otimizado para fluxos mais altos do que o mínimo, usando velocidades e turbulência suficientemente altas para superar influências externas, como ventos cruzados. Na ponta do SteamForce HC, um anel de jato é instalado ao redor do perímetro do bocal para garantir a interação adequada entre o ar de combustão e o gás flare em fluxos mínimos. Alguns fornecedores especificam pressões operacionais flare relativamente altas, como 2 a 5 psi, para atingir os parâmetros de desempenho prometidos. Essas tecnologias dependem da energia cinética dos gases em taxas de emergência ou de perturbação para otimizar o desempenho. No entanto, vários flares de vapor operam em pressões máximas mais baixas, e o desempenho dessas pontas costuma ser drasticamente prejudicado em baixas taxas de abertura de válvula. Por outro lado, um anel de jato controla a forma do fluxo flare , garantindo que ele interaja corretamente com o núcleo de ar educado, e mantém o desempenho da ponta em toda a sua faixa operacional, principalmente em plena abertura.
Considerações de custo e operacionais
Como os eventos de queima são pouco frequentes e, normalmente, de curta duração, os fluxos de vapor de resfriamento constante constituem a maior parte do vapor consumido por uma ponta do flare anualmente. O fluxo de resfriamento do vapor protege a integridade dos injetores, atenuando os efeitos do calor da zona de combustão; esse fluxo e seus efeitos negativos são exacerbados em climas mais frios. Com o projeto do SteamForce HC, essencialmente toda a indução de ar sem fumaça ocorre na base da ponta. Como resultado, os injetores não estão tão sujeitos a danos térmicos. Mais importante ainda, o maior volume de ar impulsionado pelos tubos venturi reduz ainda mais o fluxo mínimo de vapor necessário para proteger o equipamento. São necessários poucos bicos venturi para atingir capacidades sem fumaça comparáveis, reduzindo novamente os requisitos de vapor de purga (Tabela 1).
Como uma aproximação geral do tempo que um flare passa no fluxo de purga em relação a uma grande carga de alívio, a proporção de 95% para 5% tem sido razoavelmente usada no setor. Os usuários finais têm um registro da taxa máxima de injeção de vapor e do fluxo mínimo de vapor para o equipamento flare e, portanto, uma análise básica entre diferentes tecnologias demonstra como o custo operacional das pontas flare pode ser dominado pelo caso normal e mínimo. O uso de um valor geral de US$ 12/1000 lbs para a geração de vapor destaca a capacidade de economia de custos da nova tecnologia de vapor flare (Tabela 2).
O método mostrado na Tabela 2 para o cálculo do custo de operação é simplificado e capta apenas a economia de fornecimento de vapor.4 Quando os reguladores e usuários consideram adicionalmente a robustez da zona de combustão, às vezes expressa como valor líquido de aquecimento da zona de combustão (NHVcz), um fluxo de combustível enriquecedor deve ser adicionado a taxas mínimas de purga para garantir uma combustão saudável. A quantidade de injeção de gás combustível necessária está diretamente relacionada à taxa mínima de vapor, de modo que a economia operacional da tecnologia de queima da empresa pode ser ampliada ainda mais com base nos custos de combustível e nas regulamentações locais. Em particular, esse projeto propositalmente não pré-mistura o ar induzido e o gás flare antes da saída da ponta do flare e do local do piloto. A ausência de pré-mistura significa que não há necessidade de incluir o ar induzido nos cálculos de NHVcz, conforme descrito no Código de Regulamentos Federais da Agência de Proteção Ambiental dos EUA (EPA), Capítulo 1, Subcapítulo C, Parte 63, Subparte CC.3 Quando o ar de combustão é pré-misturado com o gás flare antes da saída, ele tem o efeito de diluir o desempenho da zona de combustão ainda mais do que o próprio vapor. Ao não introduzir o ar de combustão até a saída da ponta do flare , somente o fluxo de vapor deve ser enriquecido, o que economiza ao operador um custo significativo de gás combustível de enriquecimento.
Flare A longevidade da ponta também pode ser aprimorada. Os vetores de injeção de vapor e de ar são verticais, o que reduz a possibilidade de formação de chama. As tecnologias anteriores de injeção de vapor tinham uma inclinação horizontal para a trajetória do vapor. Quando os fluxos de gás flare estão em taxas mínimas, o fluxo de vapor transmite mais pressão, velocidade e momento do que o fluxo de combustível. O desequilíbrio no fluxo resulta em uma "tampa" efetiva sobre a saída da ponta do flare , e essa tampa geralmente empurra a combustão para baixo dentro do cilindro da ponta do flare . Essa reação química redutora de alta temperatura dentro da ponta causa danos irreparáveis ao longo do tempo e é um modo de falha comum das pontas assistidas por vapor. Várias fontes de injeção de vapor que exigem várias válvulas de controle podem exacerbar esse dano, pois é possível aplicar a injeção de vapor superior de forma muito agressiva em comparação com o nível aplicado por meio de tubos S/A. No entanto, quando apenas uma única fonte de vapor e controle são usados, a combinação de vetores de injeção ascendente e controle de ponto único elimina a queima interna da ponta do flare e proporciona maior longevidade e valor para a instalação ao longo do tempo.
CONCLUSÕES
Em geral, o público vê as chamas altas e brilhantes provenientes das chaminés de flare como o maior risco à saúde e ao meio ambiente. Ironicamente, essas chamas indicam alta eficiência de destruição e que o flare está quebrando corretamente os hidrocarbonetos em composições seguras. O que não foi compreendido é que os fluxos mínimos, quase despercebidos, são os mais suscetíveis à aplicação excessiva de vapor e ar. A aeração excessiva é responsável por maiores danos ambientais, e sua retificação resulta em melhorias significativas nos custos operacionais e de capital. Com a criação de um mecanismo de injeção de vapor mais eficaz, a zona de combustão é aprimorada durante o caso de uso predominante de baixa vazão e, ao mesmo tempo, usa-se menos vapor em condições de alta vazão ou de perturbação.
REFERÊNCIAS
- Make Listening Safe', Organização Mundial da Saúde, https://www. who.int/pbd/deafness/activities/MLS_Brochure_English_lowres_ for_web.pdf, (acessado em 14 de janeiro de 2019).
- 'Parameters for Properly Designed and Operated Flares', US EPA Office of Air Quality Planning and Standards, https://www3. epa.gov/airtoxics/flare/2012flaretechreport.pdf, (acessado em 14 de janeiro de 2019).
- EPA 40CFR 63.671.
- Benchmark the Fuel Cost of Steam Generation, US Department of Energy, https://www.energy.gov/sites/prod/files/2014/05/f16/ steam15_benchmark.pdf, (acessado em 14 de janeiro de 2019).