Assumindo o Enigma de Azulejo
CATEGORIAS:
David A. Short, Zeeco, Reino Unido, descreve como foi feita uma atualização no design do tradicional ladrilho de queimador de parede radiante usado em queimadores de processo.
Os azulejos queimadores de parede radiante desempenham um papel intrínseco na manutenção da temperatura do forno e da estabilidade e eficiência operacional. Historicamente, os azulejos queimadores de parede radiantes eram fabricados em quatro peças utilizando argilas de tijolos refractários, moldadas à mão, suportadas por ganchos externos de fixação lateral. Durante a década de 1970, a maioria dos azulejos radiantes para queimadores de parede foram produzidos em duas peças utilizando material convencional de sílica de alumina fundida. Um sistema de retenção das presilhas laterais e inferiores foi soldado à placa de montagem do queimador frontal (Figura 1). Este projeto foi adotado pelos principais fabricantes de queimadores de processo e, na maioria dos casos, ainda se aplica atualmente.
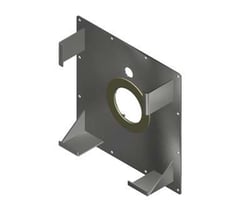
.
Entretanto, este projeto não está isento de desafios. As principais questões são o peso do azulejo e as falhas do sistema de retenção. Mesmo quando fundido em duas seções, o material refratário denso é pesado e incômodo de instalar, e requer um extenso sistema de ancoragem e suporte, como visto na Figura 1. O sistema tradicional de retenção freqüentemente permite que o gás quente penetre em torno da abertura de expansão da telha do queimador e, devido à retração ou movimento refratário adjacente, o gás de recirculação/escala não só reduz a eficiência e estabilidade do forno, como também aumenta a probabilidade de falha prematura das presilhas através do superaquecimento potencial da placa de montagem do queimador ou do invólucro do forno.
Para garantir que um ladrilho tenha o desempenho esperado, os usuários finais devem considerar critérios críticos de seleção de material refratário. Estes incluem:
- Temperatura de funcionamento do forno
- Temperatura da face fria do forno
- Queima de gás ou óleo
- Oxidando ou reduzindo a atmosfera e a composição do gás
- Queimadores montados no telhado, parede ou piso
- Probabilidade de erosão de gás e/ou ataque químico
- Probabilidade de fogo direto
- Condições de ciclismo térmico.
Um Novo Projeto de Ladrilho Modular
Os engenheiros da Zeeco se propuseram a criar uma telha com maior integridade e confiabilidade. O projeto resultante, denominado Zeecolite, é uma telha composta de uma peça única para queimadores de parede radiante (Figuras 2 e 3). Os principais componentes desse projeto incluem uma face quente resistente à erosão e um isolamento de backup de material leve e termicamente eficiente com ancoragem segura incorporada em aço inoxidável Inconel.
Figura 2. Azulejo de parede radiante composto zeecolite de uma peça - face quente.
Figura 3. Azulejo de parede radiante composto zeecolite de uma peça - face fria.
O projeto modular de uma peça utiliza um óxido férrico baixo de alumina de 62% especialmente formulado 1700˚C baixo cimento fundível como a face quente, apoiado por placas de isolamento de fibra cerâmica (Figura 4). O projeto oferece tanto eficiência térmica quanto resistência à erosão - critérios fundamentais para o desempenho do queimador e confiabilidade da caixa de fogo.
Figura 4. Vista lateral do projeto modular de azulejos mostrando placas de isolamento de fibra cerâmica e sistema de ancoragem embutido.
A montagem da telha é auto-sustentável com um sistema de ancoragem embutido em aço inoxidável Inconel de quatro pontos. O sistema embutido, totalmente fechado, é usado para fixar o módulo de azulejo ao invólucro do forno ou à placa de montagem do queimador. O sistema de ancoragem é completamente independente do refratário do forno ao redor e dos componentes de combustão do sistema do queimador. A incorporação das âncoras na seção fundida evita os problemas associados à fadiga e oxidação do metal (Figura 5).
Figura 5. Vista lateral do desenho do azulejo modular mostrando os parafusos de olho para manobrar o azulejo no lugar.
Atrás da face quente, a placa de isolamento de fibra cerâmica proporciona a eficiência térmica e reduz o peso. O módulo de telha resultante com sistema de ancoragem proporciona maior eficiência térmica e menor peso, necessidades fundamentais nos fornos modernos de hoje.
Tratando de questões de Longevidade e Início de Operação
A telha zeecolite é pré-secada para 360˚C para garantir a remoção tanto de água livre quanto de água química. Este processo nega o problema comum de rachadura térmica ou falha do azulejo durante os procedimentos de partida. O sistema de ancoragem totalmente protegido garante a integridade a longo prazo do sistema de suporte e evita qualquer movimento de avanço do azulejo em relação à ponta do gás queimador, tanto a longevidade quanto os desafios de confiabilidade comuns aos projetos tradicionais de azulejo. A adição do isolamento de baixa massa de fibra cerâmica melhora a eficiência térmica, o que também reduz os custos relacionados à energia para manter o forno operando dentro das especificações de projeto e metas de eficiência.
Aplicações
A telha modular de uma peça foi projetada para uso em aplicações de queimadores de chama plana com chama lateral em fornos de reforma primária. Tanto a seção fundida de face quente quanto a espessura da placa de isolamento de fibra cerâmica podem ser variadas com base no parâmetro particular do forno ou aplicação; este projeto é adequado para qualquer construção existente ou nova, independentemente da espessura da parede ou da composição do refratário ao redor.
Instalação
O módulo de azulejo queimador é projetado para ser fácil de instalar tanto para aplicações novas quanto para retroajustes. As ancoragens embutidas de aço inoxidável sobressaem através das placas posteriores de isolamento de fibra cerâmica para aparafusar na placa de montagem exterior. Para primeiro içar os módulos até o local de montagem na parede do forno, os parafusos de fixação são normalmente fornecidos com os conjuntos de azulejos. Uma vez no lugar, o sistema de montagem garante que as âncoras sejam capazes de suspender o módulo de azulejo queimador sem qualquer movimento devido ao torque gravitacional - o que significa que o módulo de azulejo não transmitirá nenhuma carga ou tensão significativa ao sistema de revestimento circundante. Esta é uma vantagem particular onde materiais delicados são usados para o sistema de revestimento, como os módulos de fibra cerâmica refratária (RCF). A colocação do módulo de revestimento em posição pode ser feita interna ou externamente, dependendo se o módulo é, por sua vez, fixado a uma placa de montagem do queimador ou diretamente ao revestimento do forno.
Se o padrão do parafuso de ancoragem não corresponder ao arranjo existente na placa de montagem do forno, furos adicionais podem ser feitos na placa de montagem usando uma placa modelo para localizar os furos ou, alternativamente, o módulo pode ser pré-montado em uma nova placa de montagem do queimador. Este tipo de módulo de azulejo está em uso em muitos fornos de reforma a vapor e tem proporcionado eficiência térmica e vantagens de longevidade.
Estudo de caso: Alemanha
Uma fornalha com queimadores de tiragem natural com queima lateral tinha uma espessura de parede refratária de 325 mm através da telha do queimador.
A telha original tinha uma face quente de 250 mm de espessura e usava uma placa de silicato de alumina 1650˚C, com duas camadas de fibra cerâmica e placas de silicato de cálcio adicionando outras 75 mm de espessura. A temperatura da face quente podia chegar a 1200˚C, embora para fins de comparação do projeto do ladrilho a temperatura média da caixa de fogo utilizada fosse 1100˚C. A temperatura da face fria, nas condições ambientais de 21˚C e sem vento, foi 96˚C com uma perda de calor de 936 W/m2 .
O novo material de face quente da telha era composto de 62% de alumina 1700˚C baixo cimento fundível e tinha 60 mm de espessura entre as teias de ancoragem e 160 mm de espessura através das teias de ancoragem, apoiado com 165 mm de placas de isolamento de fibra cerâmica. A espessura total do módulo era de 325 mm.
A temperatura média da face fria das seções fundíveis, com as mesmas condições ambientais, foi de 60˚C com uma perda média de calor de 410 W/m2 .
Como resultado da aplicação da nova telha, houve uma melhoria de 56% na eficiência térmica com uma redução do peso do módulo de 79 kg/telha.
Estudo de caso: Áustria
Uma fornalha com queimadores de tiragem natural com queima lateral tinha uma espessura de parede refratária de 293 mm através da telha do queimador. A temperatura da face quente podia atingir até 1200˚C, mas para fins de comparação do projeto do azulejo, a temperatura média da caixa de fogo utilizada foi 1100˚C.
A telha original tinha uma face quente de 158 mm e usava uma placa de silicato de alumínio 1650˚C, apoiada por três camadas de placas de fibra cerâmica e silicato de cálcio, totalizando assim 135 mm. A temperatura da face fria, com condições ambientais de 21˚C e sem vento, era de 77˚C com uma perda de calor de 645 W/m2 .
O novo material de face quente da telha era composto de 62% de alumina 1700˚C baixo cimento fundível e tinha 58 mm de espessura entre as teias de ancoragem e 158 mm de espessura através das teias de ancoragem, apoiado com 135 mm de placas de isolamento de fibra cerâmica. A temperatura média da face fria das duas seções fundíveis, nas mesmas condições ambientais, era 65˚C com uma perda média de calor de 468 W/m2 .
Consequentemente, uma melhoria de 28% na eficiência térmica foi alcançada com uma redução de peso do módulo de 38 kg/telha.
Conclusão
O novo projeto de azulejos reduziu o tempo de parada do forno e melhorou a longevidade do produto. Além disso, quando acoplado a uma maior eficiência térmica, sua aplicação resultou em economias notáveis nos orçamentos operacionais e de manutenção.
Figura 6. Funcionamento de queimadores de parede radiante no forno utilizando azulejo Zeecolite.
Download do artigo