.png)
Sua reviravolta ficou mais fácil
Acesse Zeeco para suas reviravoltas
Sabemos que as paradas de produção são um grande empreendimento, e é por isso que a Zeeco está tomando as medidas necessárias para tornar o processo o mais simples possível. Oferecemos uma equipe global de serviços de campo com recursos para executar todas as tarefas de manutenção relacionadas à transferência de calor, serviços de recuperação, inspeções e ajustes BMACT, pesquisas de combustão gratuitas, pesquisas com drones e relatórios conduzidos por especialistas no assunto. Escolha o site Zeeco para obter uma solução completa para seu projeto de recuperação.
Nosso Processo Comprovado de Cinco Etapas
Trabalhando extensivamente com clientes em todo o mundo, a Zeeco criou e aprimorou um processo comprovado de cinco etapas para simplificar ao máximo as recuperações, mantendo o orçamento e os prazos do projeto em mente.
Etapa 1: Pesquisa
-
- Conduzir a inspeção do equipamento no local
- Cumprir as diretrizes de escopo de recuperação da instalação (12 a 18 meses)
- Conduzir a inspeção do equipamento no local
Segunda etapa: Relatório
-
- Envie o relatório de inspeção para a instalação
- Normalmente, dentro de algumas semanas após a pesquisa de combustão
- Envie o relatório de inspeção para a instalação
Terceira etapa: Preparar
-
- Adquirir peças e contratos de serviço
- Dentro de 6 a 9 meses antes da recuperação
- Adquirir peças e contratos de serviço
Quarta etapa: Executar
-
- Realizar a manutenção do local durante a parada
Quinto passo: Concluir
-
- Fornecer a documentação necessária após a execução
- Normalmente, dentro de algumas semanas após a entrega
- Fornecer a documentação necessária após a execução
Equipe Global, Resposta Local
Nossa equipe de especialistas está estrategicamente posicionada em todo o mundo para fornecer uma resposta rápida a todas as suas necessidades ambientais e de combustão. Com décadas de experiência em sistemas flare , Oxidadores térmicos, gerenciamento de queimadores, controle de vapor e muito mais, o Zeeco é o seu balcão único para todas as suas necessidades de resposta.
ZeecoOs recursos de recuperação da empresa incluem:
- Instalação e comissionamento
- Inspeções com drones
- Flare substituição, inspeção e reparo de pontas
- Peças de reposição para qualquer sistema de combustão OEM
- Reparo, manutenção, limpeza e otimização da combustão do queimador
- Manutenção, modernização e substituição de carvão ativado da Unidade de Recuperação de Vapor (URV) e da Unidade de Combustão de Vapor (VCU)
- Inspeção de refratários e substituição de azulejos queimadores
- Estudos/optimização de engenharia
- Equipamento de combustão temporária
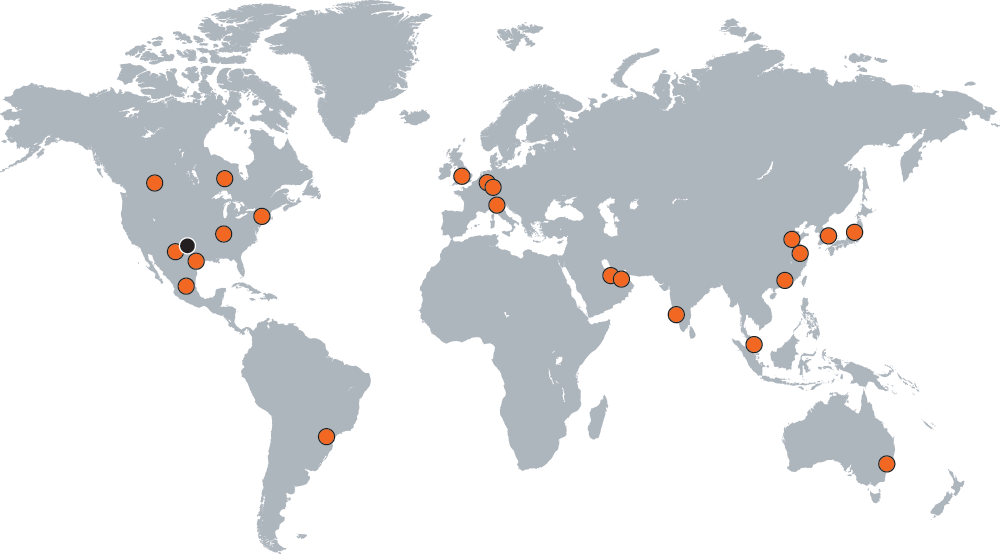
Pesquisa de Inspeção de Combustão por Amostra de Combustão
Amostra de pesquisa aérea Flare
Soluções inovadoras para problemas únicos
ZeecoA equipe de especialistas da Global Storage Inc. continua a desenvolver novas soluções para os problemas exclusivos que nossos clientes enfrentam, fornecendo a eles produtos e serviços que resolvem qualquer problema que encontrarmos. Ao longo dos anos em que trabalhamos em recuperações para clientes em todo o mundo, continuamos a expandir nossos serviços para atender a todas as necessidades de nossos clientes por meio de engenharia de modernização, inspeções aéreas, tecnologia de realidade aumentada e a criação de nossa Divisão Global de Serviços de Campo.